- Move away from the glass by stepping ten feet back.
- Face the glass straight on at 90°.
- View in the daylight but not in direct sunlight or direct applied light.
- Inspect the central 80% of the glass (examples shown below).
- Inspection should not exceed viewing of more than the following in transmission or reflection:
- 5 seconds for lites up to 6 square feet.
- 10 seconds for lites up to 35 square feet.
- 20 seconds for lites greater than 35 square feet.
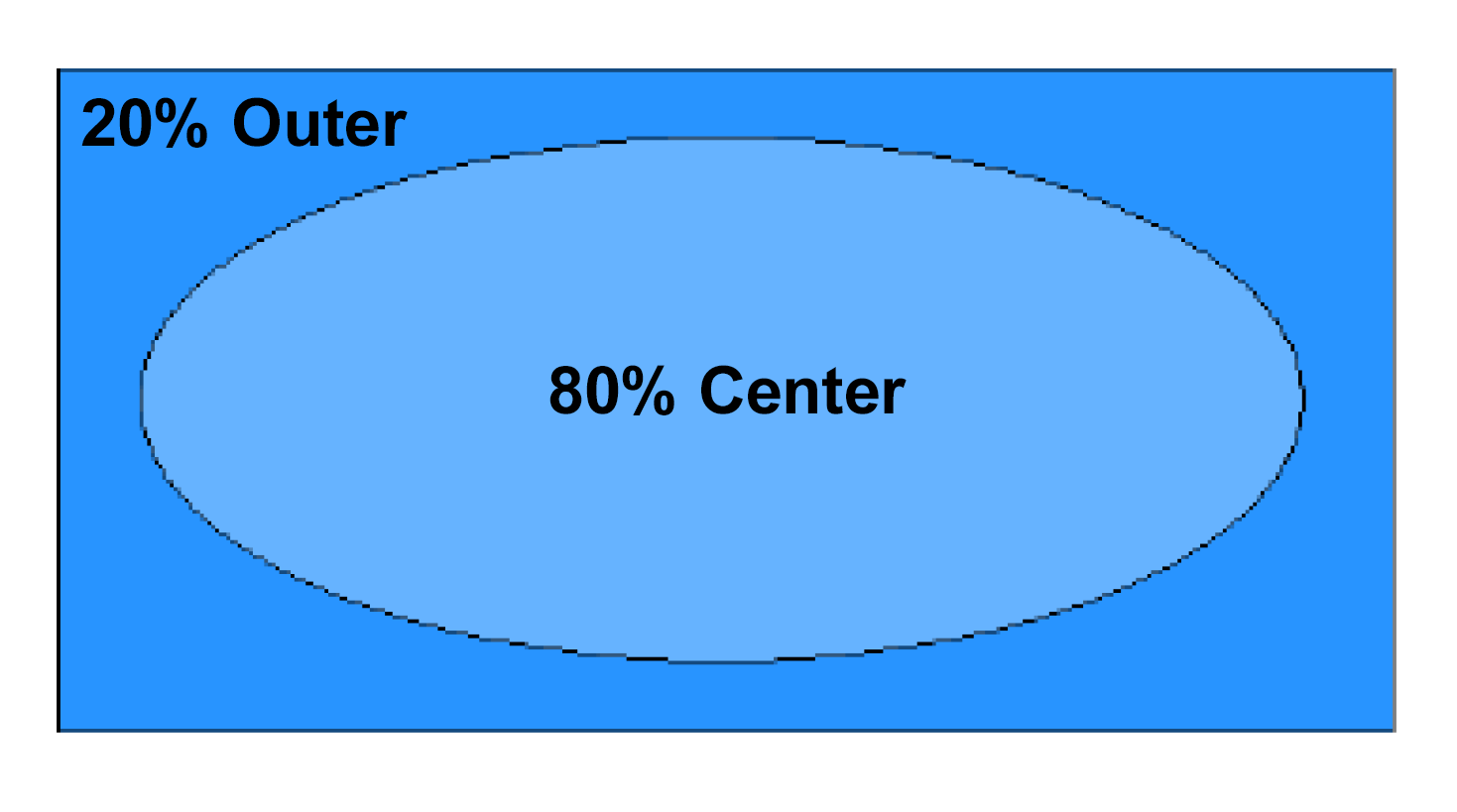
SINGLE LITES UP TO 6 SQUARE FEET
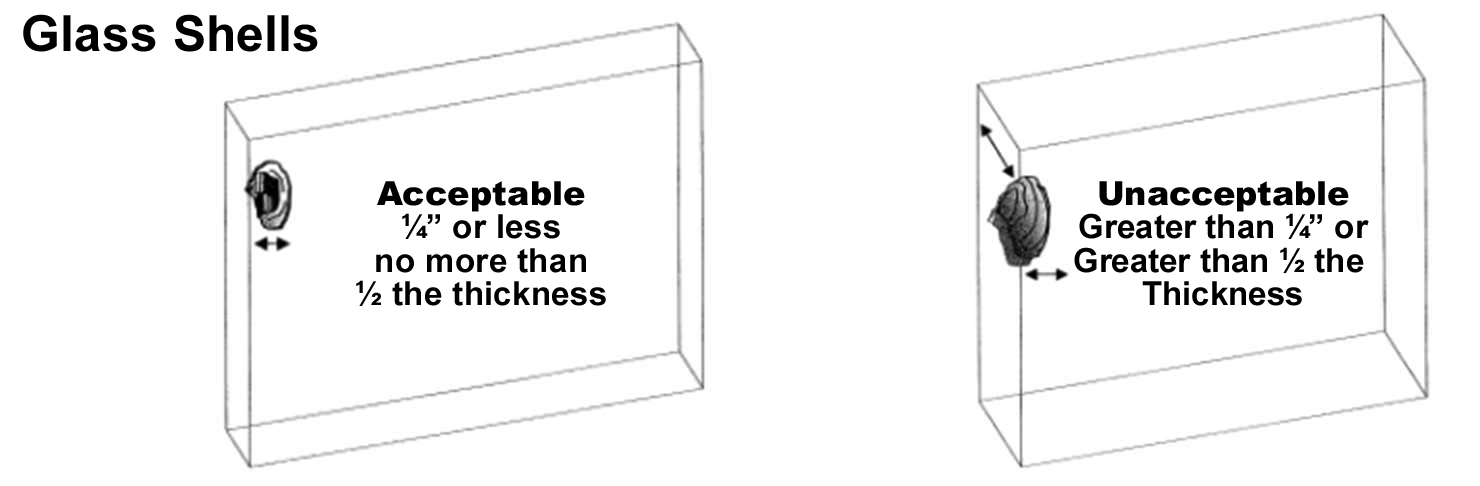

SINGLE LITES 6 TO 35 SQUARE FEET
- Scratches - Viewable as state above, must be 1" or less. No more than 2 are allowed per lite and must be separated by a minimum of 24 inches.
- Debris, Dirt, Spots - Viewable as stated above, must be 1/16" or less. No more than 2 are allowed per lite and must be separated by a minimum of 24 inches.
- Seeds, Bubbles, Knots, Stones - Viewable as stated above, must be 1/16" or less. No more than 2 are allowed per lite and must be separated by a minimum of 24 inches.
- No more than 2 total viewable defects as described above are allowed per lite.
- Shells - No more than ¼" from edge, less than ½" the thickness of the lite. No more than 1 per side.
- Chips - No more than ⅛" from the edge. No more than 1 per side (See illustration for chips).
- Coating - Must be uniform on the lite inspected when viewed in transmission using the inspection criteria previously stated above.
- The border area is made up of 4 inches plus ½" from each edge of the lite. All other areas are the central area (see illustration).
SINGLE LITES OVER 35 SQUARE FEET
- Scratches - Viewable as state above, must be 1" or less. No more than 3 are allowed per lite and must be separated by a minimum of 24 inches.
- Debris, Dirt, Spots - Viewable as stated above, must be 1/16" or less. No more than 3 are allowed per lite and must be separated by a minimum of 24 inches.
- Seeds, Bubbles, Knots, Stones - Viewable as stated above, must be 1/16" or less. No more than 3 are allowed per lite and must be separated by a minimum of 24 inches.
- No more than 3 total viewable defects as described above are allowed per lite.
- Shells - No more than ¼" from edge, less than ½" the thickness of the lite. No more than 1 per side.
- Chips - No more than ⅛" from the edge. No more than 1 per side (See illustration for chips).
- Coating - Must be uniform on the lite inspected when viewed in transmission using the inspection criteria previously stated above.
- The border area is made up of 6 inches plus ½" from each edge of the lite. All other areas are the central area (see illustration).
ALLOWABLE DEFECTS VISUAL AID
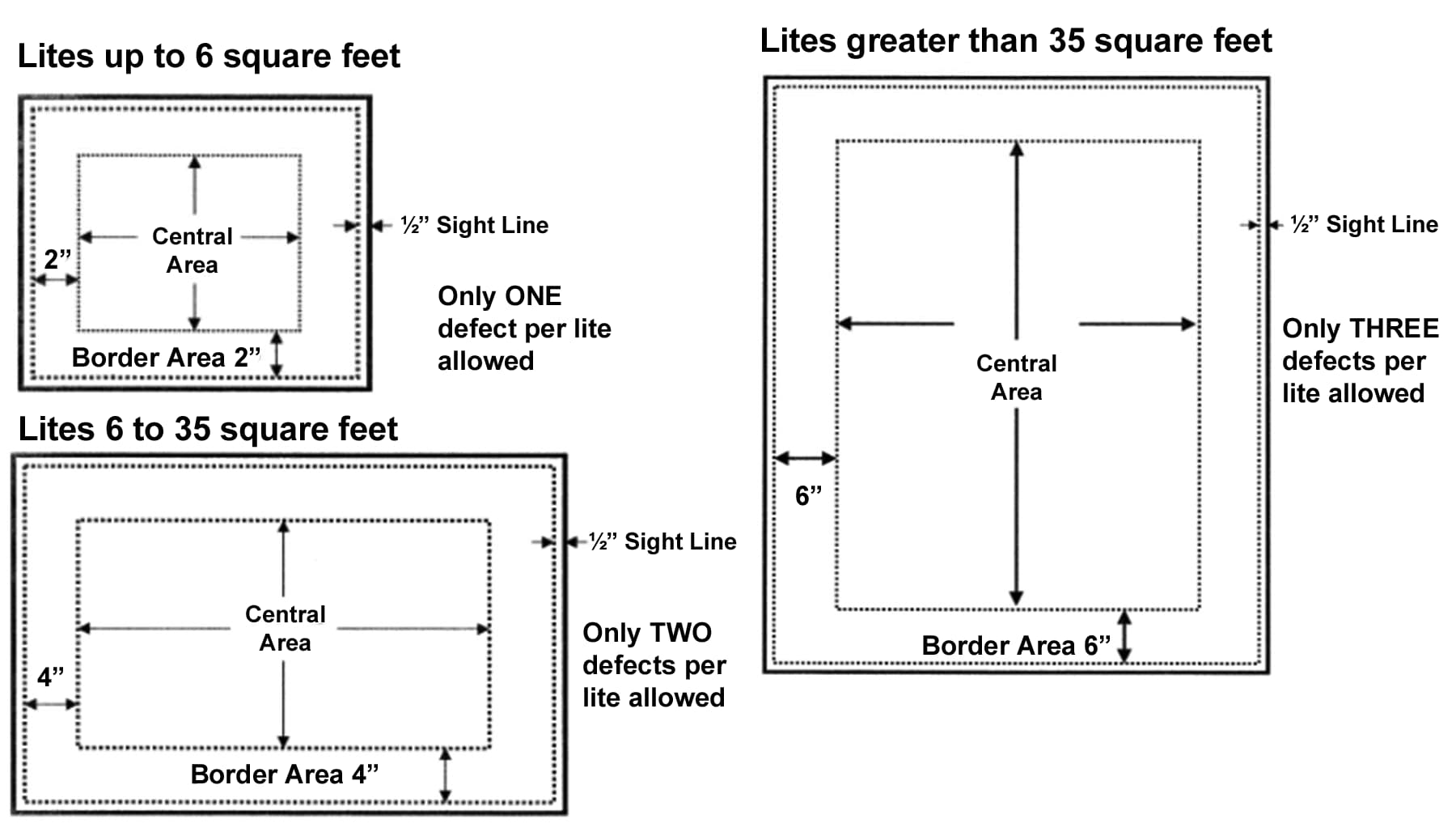
-
Type 1 (Transparent Flat Glass) - Chips on the glass edges shall be viewed at a proximity of 12" without magnification, using localized lighting.
- Shell Chips*: Shell chips are permitted within the requirements shown in Table 3, if there are no associated cracks, detectable without magnification, as viewed from the edge.
- Chip depth ≤ 50% of glass thickness.
- Chip width ≤ glass thickness or 6mm (¼"), whichever is greater.
- Chip length ≤ 2 times the chip width. * Taken from ASTM C1036-21 Table 3 Allowable Shell Chip Size and Distribution for Cut Size and Stock Sheet Qualities of Type 1 —Transparent Flat Glass (Quality-Q3) Type 1, Class 1 and 2 glass as specified by Section 4 Classification and Intended Use.
- V-Chips are not permitted.
- Dimensional Tolerances for length, width, squareness, and thickness for rectangular shapes shall use the tolerances in accordance with ASTM C1036-21 Table 4.
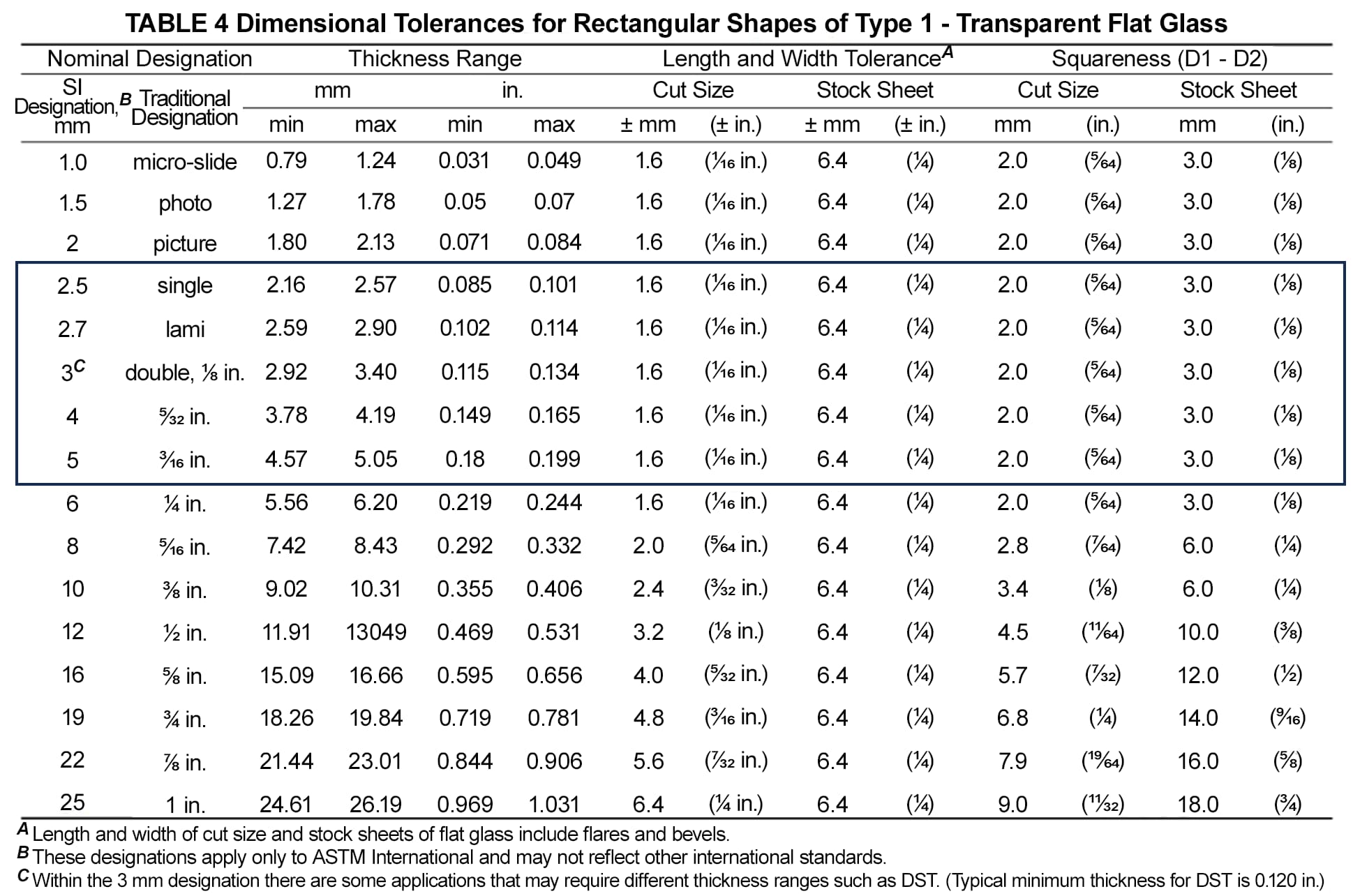